支撑辊的制作工艺流程根据其用途(如冶金轧机、汽车生产线等)和材料(如合金钢、聚氨酯复合结构等)的不同而有所差异,以下是综合搜索结果整理的主要工艺流程:一、原始制造工艺流程(以冶金轧机支撑辊为例)材料冶炼与锻造选用高铬中碳合金钢(如碳、铬)进行冶炼,确保成分均匀性56。钢锭经锻造形成毛坯,通过锻造祛除内部缺陷并优化晶粒结构6。热处理工艺退火处理:锻造后毛坯进行正火、球化退火及去氢退火,祛除内应力并改善加工性能36。调质处理:粗加工后整体淬火(油冷或水冷)+回火,使辊身硬度达45~50HSD,芯部保持韧性56。差温淬火:采用全自动数控差温淬火技术,辊身表面硬度达55~60HSD,淬硬层深度≥100mm,提升耐磨性和抗剥落性56。机械加工粗加工:铣平端面、钻中心孔,粗车外形以去除氧化层5。半精加工:调质后修中心孔,半精车辊身和辊颈,预留精加工余量6。精加工:淬火后精车、磨削至成品尺寸,表面粗糙度Ra≤μm,确保辊面精度56。表面处理与装配辊颈镀锌或喷涂防锈层,防止锈蚀2。热装轴承、止推环等部件,并进行终检验5。二、修复再制造工艺流程(以堆焊修复为例)探伤与缺陷处理通过着色探伤检测表面裂纹,超声波探伤检查内部缺陷,确定可修复区域18。 涂胶辊应用领域场景印刷与包装行业软包装复合:将多层材料通过胶水复合,用于食品、yao品包装。宝坻区印版轴
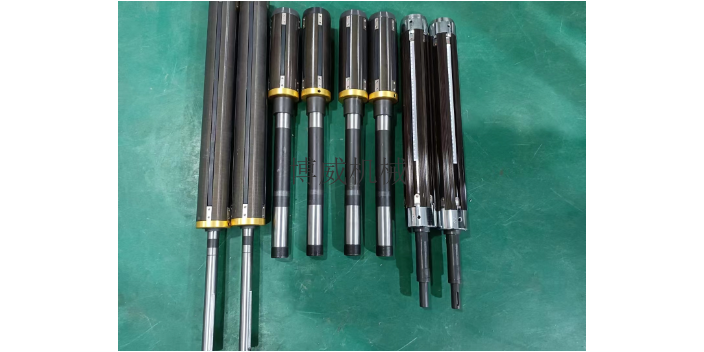
钢辊的尺寸分类主要依据其直径、长度和壁厚等参数,具体如下:直径:小直径钢辊:通常用于轻型设备,如小型输送机、印刷机等。中直径钢辊:适用于中型设备,如中型轧机、传送带等。大直径钢辊:用于重型设备,如大型轧钢机、重型输送机等。长度:短长度钢辊:适用于空间有限的设备或需要高精度加工的场景。中等长度钢辊:常见于大多数工业设备,如标准输送机、轧机等。长长度钢辊:用于大型设备或需要长距离传送的场景。壁厚:薄壁钢辊:适用于轻负荷、高转速的设备,如某些印刷机辊。中等壁厚钢辊:适用于中等负荷和转速的设备,如标准轧机辊。厚壁钢辊:用于重负荷、低转速的设备,如大型轧钢机辊。其他尺寸参数:轴径:钢辊轴的直径,影响其承载能力和安装方式。总长度:包括辊身和轴头的总长度,影响设备的整体设计。端部尺寸:钢辊两端的尺寸和形状,影响其与其他部件的连接方式。定制尺寸:根据具体应用需求,钢辊的尺寸可以定制,以满足特殊设备或工艺要求。 石景山区陶瓷轴气辊制作工艺步骤8终检检验:确保气辊符合设计要求和客户标准。
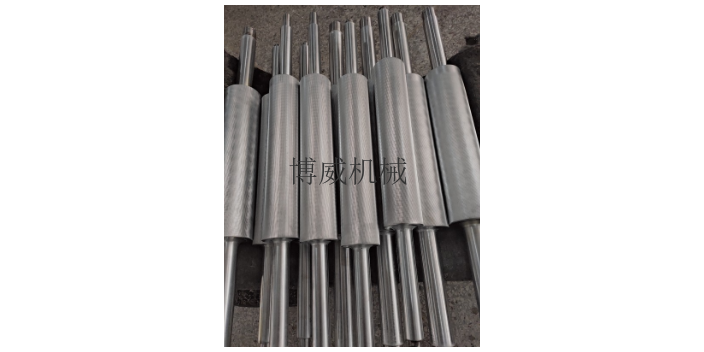
三、使用与维护难点磨损与寿命限制热轧辊长期承受高温(800–1250℃),表面易氧化、热疲劳剥落,需频繁修磨(单次磨削量–2mm),报废直径为原始尺寸的85–90%34。冷轧辊表面镀层易因摩擦损耗失效,镜面抛光要求高(Ra≤μm),维护成本高56。维护复杂与拆卸困难传统轴承内环与辊颈采用过盈配合,拆卸需机械敲击,效率低且易损坏内环;液压拉出法虽改进效率,但仍需特用工具78。卡环、滑板等附件易磨损或脱落(如焊接卡环开焊),导致换辊困难或停机事gu8。振动与稳定性问题物料细粉过多或温度过高时,辊压机易因料层不均、气泡破裂等引发振动,影响轧制精度和设备寿命4。辊面磨损后凹凸不平,加剧受力不均,导致电流波动和系统循环量失控4。四、经济性与适应性限制能耗与环bao压力传统轧辊启停能耗高,碳纤维辊虽降低重量,但材料成本昂贵,普及受限12。镀铬工艺涉及重金属污染,复合热处理(如氮化+淬火)虽环bao,但技术门槛高3。应用场景局限性铸铁/锻钢辊适用于粗轧,但难以满足极薄带钢(如锂电池铜箔)的高精度需求,需依赖碳化钨等特种材质67。高温、腐蚀性环境(如钛合金轧制)对辊轴涂层和材质提出更高要求,增加技术难度56。
5.滚珠丝杆轴功能:将旋转运动转化为高精度直线运动,用于定wei和传动。特点:摩擦阻力极小,支持高速、高精度定wei(如瓦楞纸板压线分纸机中轴向移动系统),节能效果明显6。应用:包装机械的精密裁切、分条及高速换单调整6。6.伺服驱动轴功能:通过伺服电机直接驱动,实现无机械传动的同步操控(如电子轴)。特点:取消齿轮链条结构,减少振动和磨损,支持自动偏心调整和色标追踪(如Weinview触摸屏操控系统)49。应用:枕式包装机的横封刀驱动、物料输送等环节9。7.振动盘驱动轴功能:驱动振动盘实现物料的自动排列和计数下料。特点:配合PLC或单片机操控,支持多种计数混装(如凯力KL-35LS螺丝包装机),提升自动化水平10。应用:五金螺丝、电子元件等小件产品的自动包装10。8.封切轴功能:操控封口和切割动作,确保包装密封性和尺寸一致性。特点:采用伺服电机驱动,结合温度PID操控,适应不同包装材料(如复合膜、薄膜)910。应用:食品、日化产品的封口与裁切工序910。总结包装机械中的轴类部件涵盖传动、导向、填充、放卷、封切等多种功能,其选型需根据具体工艺需求(如速度、精度、负载)及材料特性决定。高精密传动元件。 涂布辊带来的便利6. 技术创新 新材料:采用新型材料提升涂布辊性能,如耐磨、耐腐蚀材料。
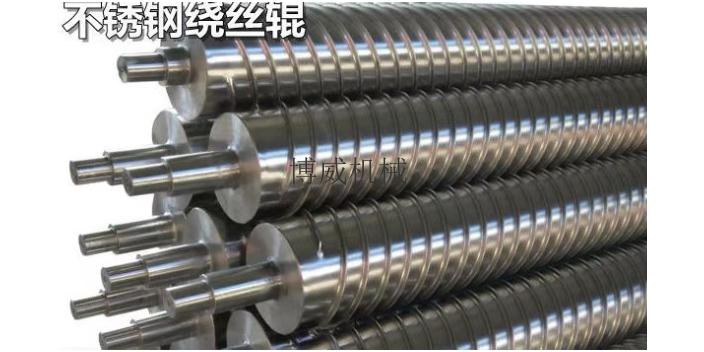
五、行业差异化工艺需求半导体主轴:洁净室装配(Class100级环境),避免微粒污染。非磁性材料加工:采用铍青铜或陶瓷轴承,防止磁场干扰晶圆搬运。yi疗微型主轴:微细电火花加工(μ-EDM):加工直径刀ju夹头,精度±2μm。生wu兼容性涂层:羟基磷灰石(HA)涂层用于骨科手术主轴。六、工艺发展趋势绿色制造:干切削工艺减少切削液使用,低温冷风技术降低能耗。再生砂轮和废旧主轴再制造技术(如山崎马扎克Eco-Processing)。数字化工艺链:数字孪生技术模拟加工过程,优化参数(如主轴转速-进给量匹配模型)。AI质检系统实时分析加工数据,缺陷检出率≥。总结主轴工艺是**“精度+材料+智能化”**的高度融合:传统工艺(如磨削、热处理)通过数控化升级实现纳米级精度;新兴技术(增材制造、激光加工)突破结构限制;行业定制化工艺推动主轴从通用件向特用化发展。未来,工艺创新将持续赋能主轴在极端工况(如深空探测、核反应堆)中的应用,成为高尚装备自主化的关键突破口。 涂胶辊应用领域场景4.汽车与工业制造 工业胶带生产:如双面胶带、遮蔽胶带的胶水涂布。宁河区胶轴
涂胶辊应用领域场景7.其他特殊场景 皮革加工:合成革的PU涂层涂布。宝坻区印版轴
“轴”在不同领域有不同的含义,因此生成方式也有所不同。以下是几种常见场景下的解释:1.机械工程中的轴(机械轴)机械轴是机械传动中的重要部件,用于传递动力或支撑旋转部件。其生成过程大致如下:设计阶段:需求分析:确定轴的用途(如传动轴、支撑轴)、负载类型(扭矩、弯矩)、转速、工作环境(温度、腐蚀性)等。材料选择:常用碳钢、合金钢(如40Cr)、不锈钢或复合材料,需考虑强度、耐磨性、耐腐蚀性等。结构设计:通过计算确定直径、长度、键槽、螺纹等细节,使用CAD软件建模并模拟受力分析。加工阶段:毛坯制备:通过锻造、铸造或直接使用棒材。切削加工:使用车床、铣床等加工出精确的几何形状。热处理:淬火、回火提高硬度和韧性。表面处理:镀铬、渗氮或涂层以增强耐磨性、防锈。精加工:磨削、抛光确保尺寸和表面光洁度。检测:通过超声波探伤、硬度测试、尺寸测量等确保质量。2.数学/数据可视化中的坐标轴在图表或坐标系中,轴用于定wei数据点,生成逻辑如下:定义坐标系:确定原点位置(如笛卡尔坐标系原点为(0,0))。设定范围与刻度:自动生成:软件根据数据范围计算轴的小zhi、大值及刻度间隔(如Matplotlib、Excel)。宝坻区印版轴
文章来源地址: http://jxjxysb.spyljgsb.chanpin818.com/bzsb/qtbzsb/deta_27797378.html
免责声明: 本页面所展现的信息及其他相关推荐信息,均来源于其对应的用户,本网对此不承担任何保证责任。如涉及作品内容、 版权和其他问题,请及时与本网联系,我们将核实后进行删除,本网站对此声明具有最终解释权。